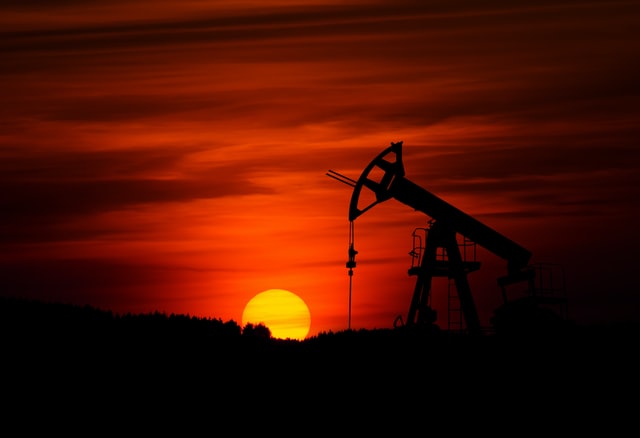
With the total operating expenses of the top mining companies worldwide reaching USD $15 billion, efficient operational methods using AI now dubbed smart mining is rapidly advancing. McKinsey estimates that by 2035, the age of smart mining achieved through autonomous mining using data analysis and digital technologies like artificial intelligence (AI) will save between $290 billion and $390 billion annually for mineral raw materials producers.
The mining industry is increasingly using artificial intelligence in innovative ways to optimize processes, enhance decision-making, derive value from data, and improve safety.
Do you know how much a mining dump or haul truck may cost?
I was speaking to a senior AI expert from Vale last week and I was intrigued by his perspectives on how expensive mining trucks are.
Did you know that a single mining truck can cost from four to over six million, and the tires alone can be more than 13-feet-tall, weighing 11,860 pounds, and each Michelin or Bridgestone tire could set you back between $40,000 to $60,000 each and typically six tires are needed.
Now those are expensive tires.
The economics of a mining truck ensuring it is safe and also can predict accidents before they happen is an interesting AI use case.
Haul trucks are crucial in getting the deposit material to the processing center. The trucks make up the largest percentage of assets responsible for mining extraction with over 40,000 in use globally. These trucks are one of the most expensive assets for mining organizations to purchase and operate.
Annual maintenance is critical for safety and in reaching ideal haul truck utilization; It is also incredibly expensive. A few factoids:
- Original equipment manufacturers (OEMs) provide standard maintenance guidelines every 500 service hours
- Engine valve inspections every 3,000 service hour
- Fuel injector changes every 6,000 service hours
- Full service every 10,000 service hours
- Engine replacement every 20,000 service hours
AI can be used in very powerful ways to predict wear and tear on trucks, and evaluate all the mechanical behaviors in an intelligent centralized system which monitors everything remotely.
These sophisticated AI intelligence systems can help mining companies in a number of ways:
Acquire Data – live streaming data from engines, equipment and machines
Convert Data- read and translate protocols and formats to the required protocols
Transmit Data- putting data into other systems
Analyze Data- Development of edge (on the machines) and cloud & visual analytics
Visualize Data- Browser Dashboard(s) for end users to visually see and interact with data in a useable format
Smarter Mines is an exciting area in applying Artificial Intelligence with Sensors and Data Analytics.
One of the companies to watch is Huawei’s Mine Brain solution which can boost safety in coal mines by optimizing workplace and supervisory efficiency. It can also replace humans in hazardous environments and take on tedious and repetitive tasks. For example, Mine Brain’s computer vision capabilities can monitor scraper conveyors, reducing the number of people needed and increasing efficiency. For example, a coal mine in Inner Mongolia with an annual output of 21.7 million tons requires 900 people. At the moment, 10 scraper machines are operated simultaneously for underground digging. One person is needed per shift to perform specialist start-stop operations for each machine meaning that 10 people are required per shift and 30 for three shifts. Replacing those 30 workers with equipment could save 6 million yuan (around US$837,160) a year based on an annual cost of 200,000 yuan per worker.
Mine Brain also uses computer vision to report unsafe behavior to the onsite monitoring system, which can then issue warnings. The solution can monitor the state of workplace objects and environment and predict risks like people working in front of shearers or missing hydraulic support guard plates, and issue warnings and maintain safety records.
It is not too hard to imagine a future world where all mining operations will be managed by a centralized intelligent system like Mine Brain is developing where every move is recorded, predicting machine risks, people behavior risks, safety risks and ensuring all operating costs are optimized.